Getting PCBs manufactured is
traditionally a somewhat laborious process. Parker Dillmann, lead EE and
co-founder of MacroFab, aims to take some of the old-school pain out of
product development and scaling processes. AAC spoke with Parker
recently to talk about old issues and new innovations in PCB design and
fabrication.
MacroFab was founded four years ago with the idea that these portions of the design process should be faster, more accessible, and intuitive. Using software-driven methods, MacroFab is trying to change the way engineers interact with PCB fabrication, from prototypes to scaling.
AAC recently got in touch with Parker Dillmann, co-founder and lead EE of MacroFab. Along with his work on MacroFab, Parker also runs The Longhorn Engineer, a site for his personal designs that shares a glimpse into his ongoing adventures and love of hardware through tutorials and guides.
We asked Parker about how his career brought him to PCB manufacturing, what industry trends have affected PCB design, and what mistakes he most often sees engineers make.
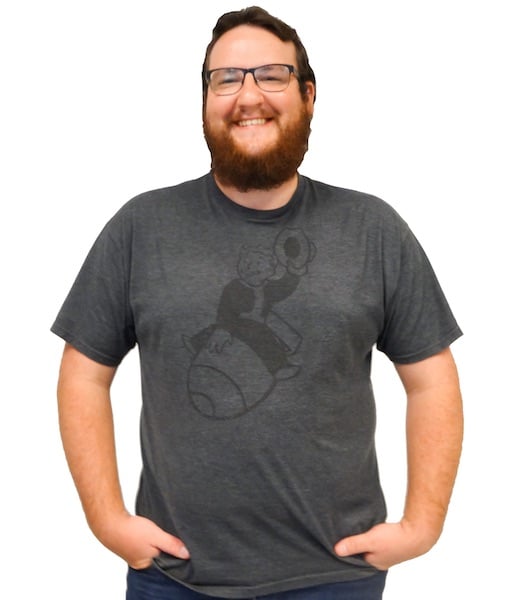
Parker Dillmann, Lead EE and Co-Founder of MacroFab.
All About Circuits: The way you got your start in electronics was hacking Nintendo and Atari consoles, right? What are some of the skills or lessons you’ve learned from those projects and your work on the Long Horn Engineer website?
Parker Dillmann: The first thing I learned was to analyze PCBs and figure out how the hardware worked. Early on, it was rare to find a schematic of these older gaming consoles, let alone learn how they functioned. Also, by taking apart these consoles, you start to learn how products are designed and you get a good sense of how they are assembled. Learning about soldering, multimeters, oscilloscopes, and digital logic analyzers all happened by reverse engineering these consoles.
The second thing was learning how to create my first PCB. I designed an audio-video mod for the Atari 2600 that became popular. The first versions were made on protoboard but that did not scale very well. I taught myself how to use the “FreePCB” design tool and created my first set of Gerbers and shipped them off to a PCB fab.
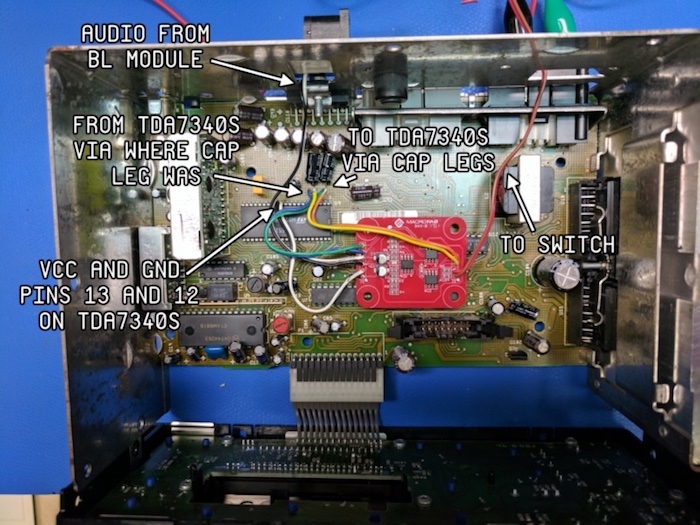
A screenshot from one of Parker's posts on The Longhorn Engineer.
AAC: What drew you to circuit design and board layout as opposed to other areas of electrical engineering?
PD: Circuit design and PCB layout were some of the first things I did before even going to school for electrical engineering so that will probably be the reason. I always wanted to design and build new products and circuits.
AAC: It isn’t exactly a typical career path for an EE to start a PCB manufacturing company. Has your work been leading up to MacroFab your whole life or was this an opportunity that came up somewhat suddenly?
PD: Actually even before that it was weird! I started out in school as a Petroleum and Geosystems Engineer. After taking my first rock formations class, I realized that was not for me. At the time, I had already created my first couple PCBs and was starting to get into C programming for microcontrollers so I decided to switch majors into Electrical and Computer Engineering.
After college, I went to work in the oil field as an Instrumentation and Electronic technician until I found an engineering job working for Dynamic Perception. I designed embedded hardware and firmware there until one of the founders of that company, Chris Church, decided to start MacroFab and I decided to start MacroFab with him.
AAC: What were some of the main problems you saw in electronics manufacturing before starting MacroFab?
PD: At Dynamic Perception, one of the biggest problems we saw was getting low-to-mid volume electronics made. Most contract manufacturers made you sign long-term contracts and agree to production runs. This does not really fit with startups or small businesses that need to quickly iterate products to add features.
We also wanted more transparency in the manufacturing process and a better breakdown of the process and pricing which would allow us to tweak our designs to be easier and less expensive to manufacture. MacroFab was born to solve these problems.
We wanted more transparency in the manufacturing process and a better breakdown of the process and pricing which would allow us to tweak our designs to be easier and less expensive to manufacture.
Our online quoting interface allows users to see what parts cost for their PCB assembly. The platform allows customers to check the status of their PCB assembly and our unique tools allow affordable high mix low volume manufacturing, which is helpful for startups and small businesses. We also do high volume manufacturing for companies who want to go to market or want to introduce a new product to market.

A screengrab of a design on the MacroFab platform.
That’s one of the great things about MacroFab—we’re more than a prototype shop, so as your company grows, you don’t have to switch manufacturers to scale your growth; you can stay with us all the way to production, maintaining a single relationship with one CM.
AAC: You’re in a unique position to see how industry trends affect design. What trends in the past few years have changed PCBs the most in the last few years?
PD: The largest trend I have seen is the push by component manufacturers to SMT-only (surface-mount technology) parts and more recently the push to BGA (ball grid array), QFN (quad-flat no-leads packages), and DFN (dual-flat no-leads packages). This is likely due to smartphone manufactures being the largest part of the consumer electronics market.
Another trend I have seen is the usage of pre-certified FCC modules for Wi-Fi and BlueTooth connectivity. These are typically in IoT-type devices. The current trend, however, is the consolidation of passive chip parts like surface-mount capacitors. Manufacturers seem to be condensing their library of passive parts and also shrinking the size of the packages at the same time.
AAC: In this industry, there are always new emerging trends like flexible circuits and upcoming semiconductor materials like SiC and GaN. What’s the next big thing that will change the way EEs design PCBs?
PD: I think the next big thing is going to be the introduction of SiP (System-in-Package)-style components and rigid flexible substrates for products.
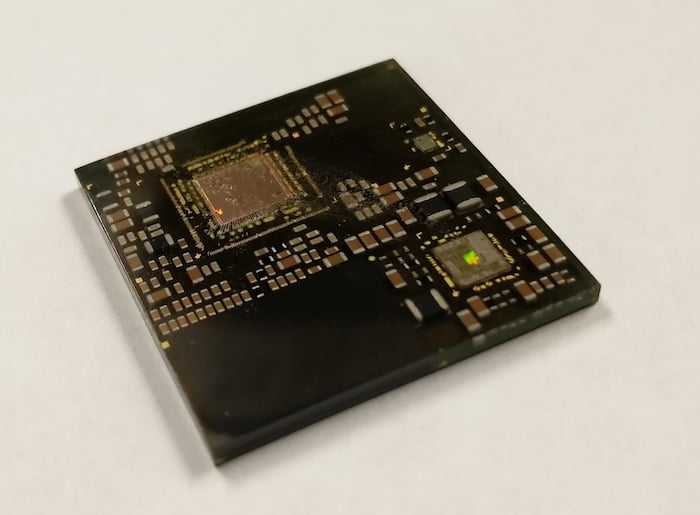
An example of an SiP, the OSD3358 from Octavo Systems. Image courtesy of MacroFab.
SiP components will drastically reduce the time to market required for products, similar to how precertified FCC modules did. As prices come down for rigid flexible substrates, we will probably see them used in more products, which will reduce the use of internal wiring harnesses and assembly labor.
SiP components will drastically reduce the time to market required for products, similar to how precertified FCC modules did.
AAC: Do you have any tips for fellow engineers trying to speed up the fabrication process for their own PCBs?
PD: Use as many SMT components as possible. SMT connectors can be done if the connector is only going to be interface during product assembly (like attaching an internal lithium battery during product assembly). SMT assembly is much faster and less expensive, labor-wise. Optimizing for SMT assembly is the number one way to optimize for production.
Also, consolidating the number of suppliers your components come from and keeping an eye on lead times for parts. Long lead times on parts can be solved by having good part substitutions.
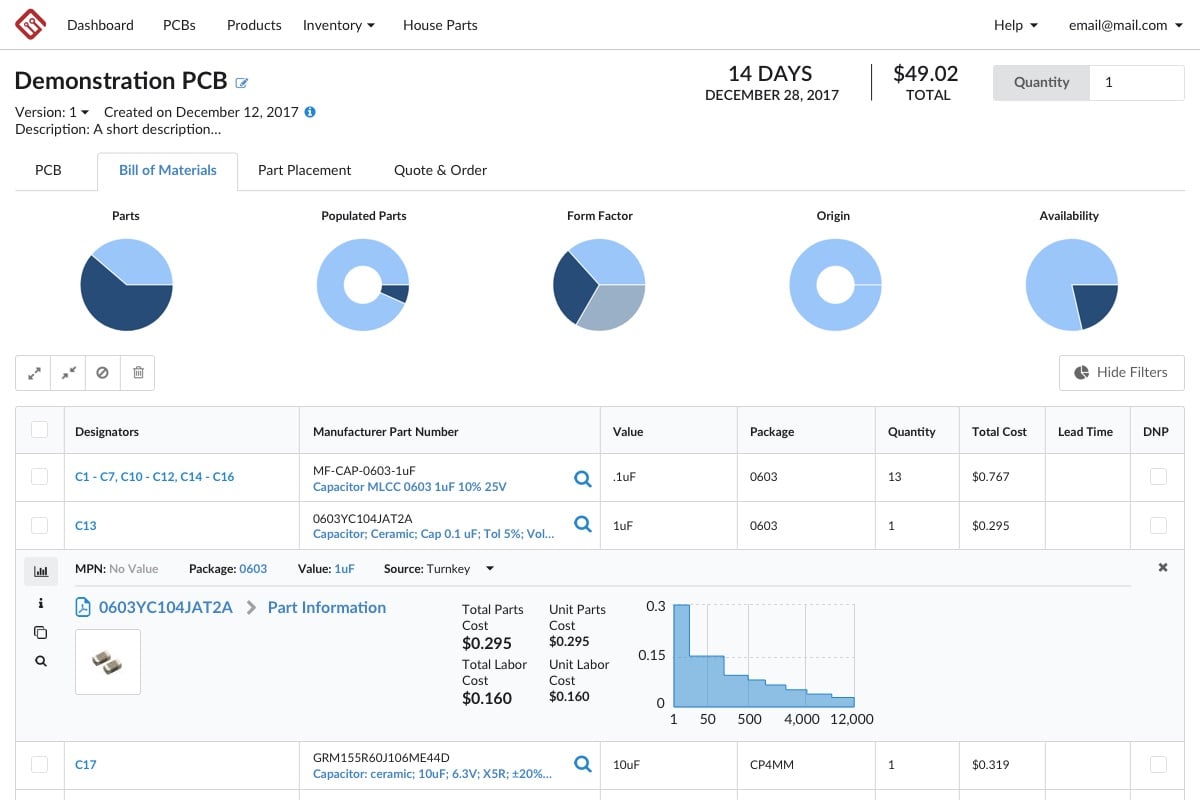
MacroFab's BOM tool.
Finally, you should optimize for post-PCB assembly, which is the next step that can be taken to speed up production. This includes build box and programming your device. Using test fixtures and programming cables like tag-connect should be thought about when designing your PCB.
AAC: Most engineers have faced some kind of issues when submitting PCB designs. What are some common challenges you've seen?
PD: There are two big ones I can think of. The first challenge that most electrical engineers face is making sure the footprint designed on the PCB is correct for the part the engineer has specified. The old school way of printing out your PCB 1:1 scale and then overlaying your parts only goes so far nowadays with parts shrinking every year. Double check your footprints always!
The second challenge is supply problems for the product’s bill of materials. Having a robust selection of part substitutions will ensure that your product will get built without delays. When searching for parts, always be sure of the expected lifetime of the product you are developing—and make sure those parts will be around for at least that long.
When searching for parts, always be sure of the expected lifetime of the product you are developing—and make sure those parts will be around for at least that long.
AAC: Are you working on anything particularly exciting that you’d like to share with our readers?
PD: Yeah, besides the projects on my personal blog, I co-host a podcast called the MacroFab Engineering Podcast along with Stephen Kraig. The “MEP” is a weekly electronics-focused podcast that goes into the projects we’re working on, both individually and collaboratively and we cover EE industry news. It's a non-serious look into the lives of two electrical engineers.
As MacroFab continues to grow, we're also looking at improving our current offerings to our customers and increasing the number of tools available to them in our online interface. We want to give our customers one place to manage every aspect of their product’s production. This includes validating and qualifying products in an interactive online interface. We are also making sure that there is always available capacity when it is needed, no matter the quantity.
No comments:
Post a Comment