From the typical pick-and-place down to the high-precision cobots, industrial robotics are changing rapidly.
There has been astonishing progress in the field of robotics, and the future is here.
On a factory floor, you won’t see any robots running or jumping like the Boston Dynamics bots. But you will see them freeing humans from dangerous, boring, and repetitive tasks—and doing them flawlessly and without error.
The National Institute of Standards and Technology recently posited that there are four types of robots that most relevant for manufacturers. Let's take a look at them from the perspective of the electrical engineer.
Articulated Robots
Articulated robots can be classified by how many points of rotation they have, with some devices having as many as seven degrees of freedom. The mechanical sophistication of these units makes them relatively expensive, and somewhat slower than other types.
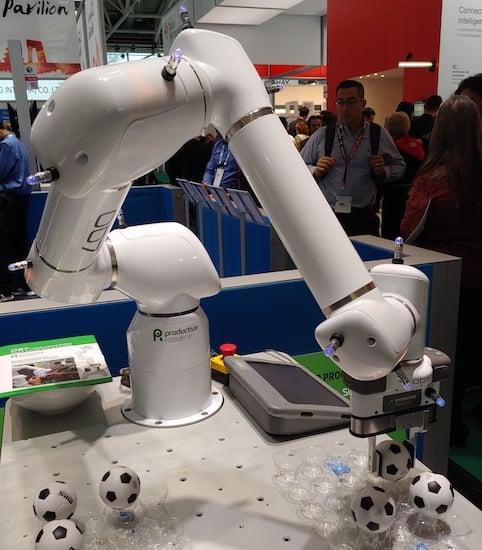
The OB7 Productive Robotics articulated robot arm. Image by Kate Smith.
Their advantages lie in the way they can move around obstacles that would block other types of robots. Perhaps the most common type in use today, these devices find use in:
- Pick and place
- Dispensing
- Packaging
- Assembly
- Welding
In the Productive Robots OB7 arm pictured above, each LED indicates the location of a Monolithic Power Systems position sensor that helps guide the arm across its tasks (in this case, gently moving small soccer balls from tray to tray).
SCARA Robots
SCARA (Selective Compliance Articulated Robot Arm) robots are selectively compliant. They can move along their x-axis and y-axis but are locked in place along their z-axis.
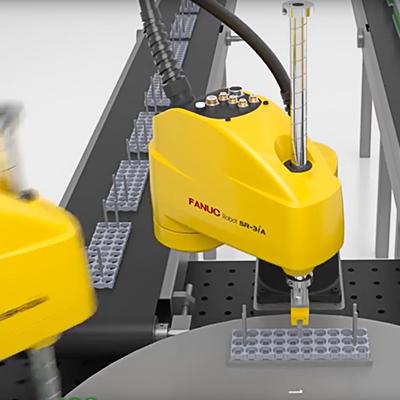
SCARA robot. Image from FANUC
Of course, fewer degrees of freedom means a less complex robot with fewer motors. The control calculations, and thereby the control algorithms, are simpler and require less computer power to implement. The smaller number of axes between the base and the part being manufactured also means that there is generally less accretion of cumulative error.
An important consideration in factory-floor robotics is how far out from its base a robot can work when compared to the floor space the base itself takes up. Nothing beats a SCARA robot here, even though they often take up less space on a factory floor.
What this all adds up to is a faster, cheaper, more accurate robot that is easier to control, despite its comparatively limited capabilities.
Delta Robots
The delta robot’s base is the triangle with a motor on each of its leg. It is situated above the workspace, as depicted in the illustration below. Each motor is hinged to one leg, the other end of the leg is hinged to the bottom triangle. The motors can be controlled by an MCU, and the nature of the geometry is such that the bottom triangle cannot swerve, like the articulated motor described above. But it can move in the x-, y-, or z-axis.
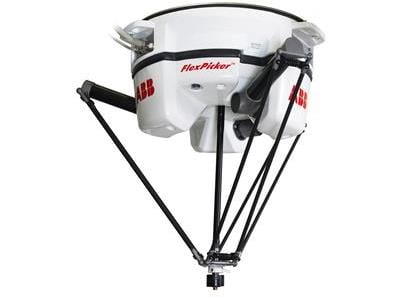
An example of a delta robot. Image used courtesy of ABB Flexible Automation
The three legs can be very light, with the only real weight being in whatever tooling part is being put in motion by the robot. Light weigh mean less inertia, so the delta robot is fast. An important use for these types of robots is in 3D printing.
Cartesian Robots
Cartesian robots are called such because they move directly across the three axes, length, width and height. Because of the inherent ruggedness of this structure, it can be used with the heaviest loads.
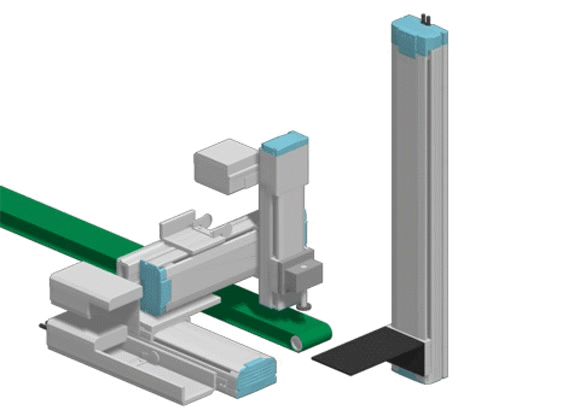
Gif of a Cartesian robot at work used courtesy of Yamaha
The difference between Cartesian robots and SCARA robots is the ability to move on the z-axis. According to Yamaha, these industrial robots can be used for pick-and-place, assembly, and even dispensation of materials such as adhesive.
COBOTs (Collaborative Robots)
As described by the International Federation of Robotics (IFR), collaborative industrial robots (COBOTS) are designed to perform tasks in collaboration with humans in industrial sectors. According to the IFR, that cooperation takes place at four levels :
- Separate cells: Human and robot work close by, but in separate physical workspaces. There is no human-robot contact or synchronization.
- Sequential collaboration: There is some intersection between the human’s and the robot’s workspace. However, one actor’s action only begins after the other’s action is complete.
- Cooperation: Human and worker work on the same part at the same time.
- Responsive cooperation: Robot responds in real-time to the human’s movements.
These levels are illustrated below. The green area represents the robot’s workspace, and the yellow area the human worker’s workspace.
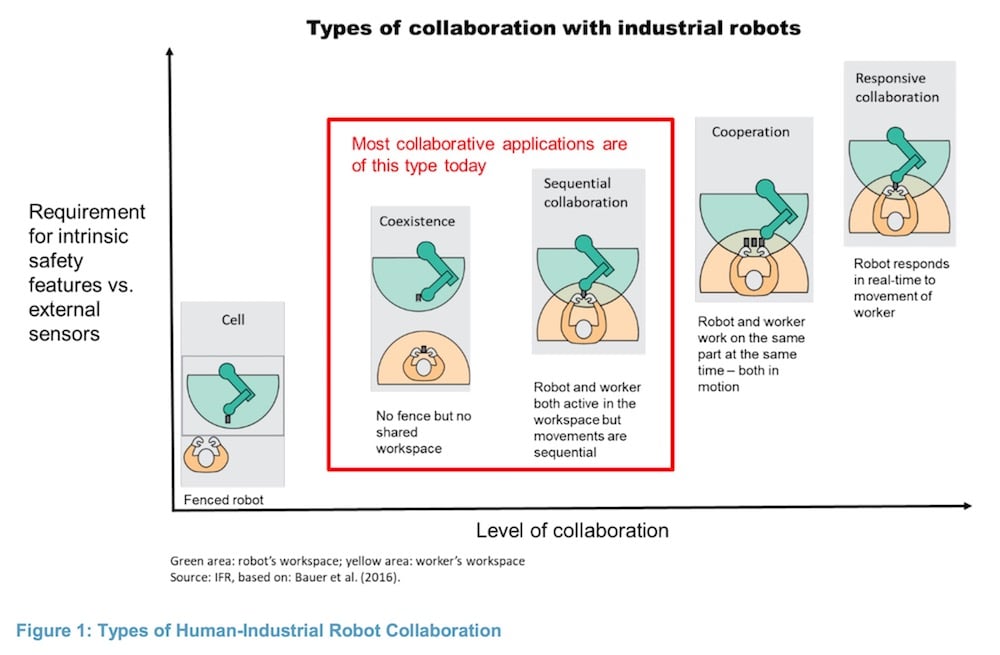
Types of collaboration with industrial robots. Image used courtesy of the International Federation of Robotics
Sequential collaboration is the most advanced level that is generally practiced in today’s factories. It would almost certainly require machine vision and artificial intelligence to implement. The robot might do something that a person would find boring or that might present a health hazard to a human. Once the robot does the dirty work, the human takes over.
What's Next? Upping Precision
A tangential branch of collaborative robots are those used in surgical applications, such as the first robotic eye surgery, performed in 2016. Perhaps the most famous of these are the da Vinci robotic surgery systems from Intuitive Surgical, which the developers don’t define as cobotic in nature, though they seem to fit the bill. The robots every move is controlled by the surgeon, but with a level of precision that no human hand can approach.
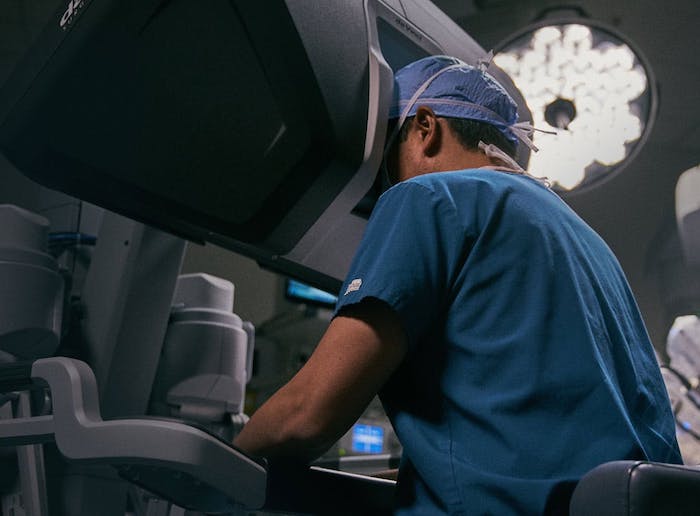
A Surgeon Console element of the general surgery setup for robotic surgery. Image used courtesy of Intuitive Surgical
With robotic control, the surgeon can operate through much smaller incisions, leading to less invasive surgeries and faster patient recovery.
Obviously, this level of precision and fine motor control could have myriad applications in industrial settings. The cost associated with these technological marvels, however, currently put them out of reach for the average manufacturing facility.
No comments:
Post a Comment