
The C-130 Hercules primarily performs the intratheater portion of the airlift mission. The aircraft is capable of operating from rough, dirt strips and is the prime transport for paradropping troops and equipment into hostile areas. Basic and specialized versions perform a diversity of roles, including airlift support, DEW Line and Arctic ice resupply, aeromedical missions, aerial spray missions, fire-fighting duties for the US Forest Service, and natural disaster relief missions. In recent years, they have been used to bring humanitarian relief to many countries, including Haiti, Bosnia, Somalia, and Rwanda.
Four decades have elapsed since the Air Force issued its original design specification, yet the remarkable C-130 remains in production. The turbo-prop, high-wing, versatile "Herc" has accumulated over 20 million flight hours. It is the preferred transport aircraft for many US Government services and over 60 foreign countries. The basic airframe has been modified to hundreds of different configurations to meet an ever-changing environment and mission requirement. The C-130 Hercules has unsurpassed versatility, performance, and mission effectiveness. Early C-130A, B, and D versions are now retired.
C-130 Missions & Variants
Missions | Specialized Variant |
---|---|
Tactical Airlift | All |
Aerial Tanker | KC-130B, KC-130F, KC-13H, HC-130H(N), HC-130N, HC-130P, KC-130R, KC-130T |
Command & Control | EC-130E (ABCCC), EC-130G, & EC-130Q |
Maritime Patrol | C-130H-NP/PC-130H |
Special Operations | MC-130E & MC-130H |
Search & Rescue | SC-130B/HC-130B, HC-130E, HA-130H, HC-130H(N), HC-130N, & HC-130P |
Humanitarian Relief | All |
Staff/VIP Transport | VC-130B & VC-130H |
Reconnaissance | RC-130B |
Airborne Hospital | C-130E (AEH) |
Arctic & Anarctic Support | C-130BL/LC-130F, C-130D, LC-130H, & LC-130R |
Drone Control | GC-130A/DC-130A, DC-130E, & DC-130H |
Electronic Warfare | EC-130E (CL), EC-130E (RR), EC-130H |
Space & Missile Operations | JC-130A, JC-130B, & NC-130H |
Test & Evaluation | NC-13A, NC-130B, JC-130E, NC-130E, JC-130H, & RC-130S |
Weather Reconnaissance | WC-130B, WC-130E, WC-130H |
Gunship | AC-130A, AC-130E, AC-130H, & AC-130U |
The C-130B introduced Allison T56-A-7 turboprops and the first of 134 entered Air Force service in April-June 1959. The B model carries additional fuel in the wings, and has upgraded engines and strengthened landing gear. C-130B's are used in aerial fire fighting missions by Air National Guard and Air Force Reserve units. Six C-130B's were modified in 1961 for snatch recovery of classified U.S. Air Force satellites by the 6593rd Test Squadron at Hickam Air Force Base, Hawaii.
Several A models, redesignated C-130D, were modified with wheel-ski landing gear for service in the Arctic and for resupply missions to units along the Distant Early Warning line. The two main skis are 20 feet long, six feet wide, and weigh about 2,000 pounds each. The nose ski is 10 feet long and six feet wide. The D model also has increased fuel capacity and provision for jet -assisted takeoff. The D models were flown by the Air National Guard and were recently replaced with C-130H models.
C-130E is an extended-range development of the C-130B, with two underwing fuel tanks and increased range and endurance capabilities. A total of 369 were ordered for MAC (now AMC) and TAC (now ACC), with deliveries beginning in April 1962. A wing modification to correct fatigue and corrosion on USAF�s force of C-130Es has extended the life of the aircraft well into the next century. Ongoing modifications include a Self-Contained Navigation System (SCNS) to enhance navigation capabilities, especially in low-level environments. The SCNS incorporates an integrated communications/ navigation management system that features the USAF standard laser gyro inertial navigational unit and the 1553B data bus; installation began in 1990. Other modifications include enhanced station-keeping equipment, 50 kHz VHF Omnirange/lnstrument Landing System (VOR/ILS) receivers, secure voice capability, and GPS capability. Another major modification installs a state-of-the-art autopilot that incorporates a Ground Collision Avoidance System. Military Airlift Command is the primary user, with more than 200 E models. The Air Force Reserve and Air National Guard also fly the E model.
Similar to the E model, the C-130H has updated T56-A-T5 turboprops, a redesigned outer wing, updated avionics, and other minor improvements. The C-130E/H carries 6,700 gallons of fuel in six integral wing tanks. Under each wing of the C-130E/H is an external pylon fuel tank with a capacity of 1,300 gallons. A pressure refueling point is in the aft side wheel well fairing for ground refueling. As a response to the role played by the tactical airlift fleet in Operation Just Cause and in the Persian Gulf War, Congress approved the procurement of more C-130H's to replace the aging E models. Delivery began in July 1974 [other sources state April 1975]. More than 350 C-130Hs and derivatives were ordered for active and reserve units of the US services, including eight funded in FY 1996.
Production of the H has now ended. Units in Military Airlift Command, the Air National Guard and Air Force Reserve are equipped with this model. The Night Vision Instrumentation System was introduced from 1993; TCAS II in new aircraft from 1994. ANG and AFRC C-130Hs are used in fire-fighting missions. Specifically modified aircraft are used by the 757th AS, AFRC, based at Youngstown-Warren Regional Airport ARS, Ohio, for aerial spraying, typically to suppress mosquito-spread epidemics. Seven LC-130Hs, modified with wheel-ski gear, are operated by ANG�s 109th AW in support of Arctic and Antarctic operations.
While continuing to upgrade through modification, the Air Force has budgeted to resume fleet modernization through acquisition of the C-130J version. Compared to older C-130s, the C-130J climbs faster and higher, flies farther at a higher cruise speed, and takes off and lands in a shorter distance. This new model features a two-crew-member flight system, 6,000 skip Allison AE 21 00D3 engines and all-composite Dowty R391 propellers, digital avionics and mission computers, enhanced performance, and improved reliability and maintainability. Beginning in FY 1996, the Air Force started procuring C-130Js as replacements for the older C-130Es and Hs. Priority for replacement will be combat delivery aircraft. C-130J will ensure total force structure numbers are maintained, while reducing costs of ownership. The current program procures 12 C-130Js, i.e., two per year from FY96 to FY01. This program could be expanded in FY02 to procure 12 C-130Js a year to replace the active duty and ARC C-130Es which are nearing the end of their useable service life.
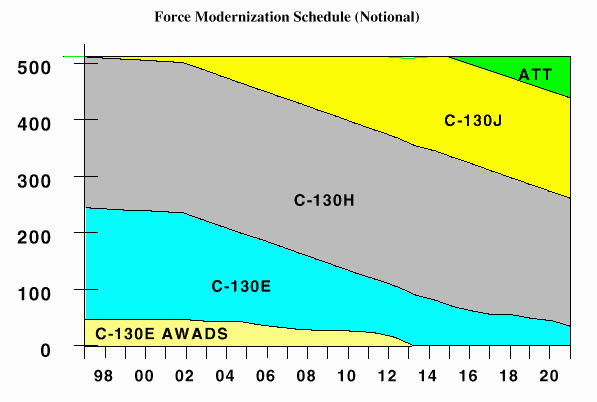
The HC-130 is an extended-range, combat rescue version of the C-130 transport aircraft. Capable of independent employment in the no-to-low threat environment. Its primary mission is to provide air refueling for rescue helicopters. The HC-130 can perform extended searches in a permissive environment and has the capability to airdrop pararescuemen and survival equipment to isolated survivors when a delay in the arrival of a recovery vehicle is anticipated. Flights to air refueling areas or drop zones are accomplished at tactical low altitude to avoid threats. NVG-assisted, low-altitude air refueling and other operations in a low-threat environment are performed by specially trained crews. The crew can perform airborne mission commander (AMC) duties in a no-to-low threat environment when threat conditions permit. The maximum speed is 290 knots (at high altitude), with a low-altitude cruise speed of 210 to 250 knots. Range, depending upon internal fuel tank configuration, is 3,000 to 4,500NM (no wind).
The C-130 Avionics Modernization Program (C-130X AMP) will modify approximately 525 aircraft to establish a common, supportable, cost effective baseline configuration for AMC, ACC, ANG, AFRC, PACAF, USAFE and AFSOC C-130 aircraft. The contractor will design, develop, integrate, test, fabricate and install a new avionics suite for approximately thirteen variants of C-130 Combat Delivery and Special Mission models. The installation schedule requires a throughput of between 65 and 85 aircraft per year through 2010. The acquisition strategy is currently in development. The C-130 AMP is being worked jointly by Warner-Robins ALC (GA) and Aero Systems Center (OH) (virtual SPO) with the Development System Manager located at ASC.
C-130J
The C-130J incorporates state-of-the-art technology that significantly improves performance and reduces ownership costs. Lockheed Martin projections show the C-130J/J-30 will lower cost of ownership as much as 45% depending on the scenario used. Early model C-130s require more than 20 maintenance manhours per flight hour (MMH/FH). The C-130J/J-30 will require 10 or less MMH/FH. The C-130J/J-30 integrated digital technology provides the capability to airdrop in instrument conditions without zone markers, as a baseline feature of the aircraft. When the high resolution ground mapping capability of the APN-241 Low Power Color Radar is coupled with the dual INS/GPS and digital mapping systems, the C-130J/J-30 provides single-ship or formation all weather aerial delivery. This means the entire J/J-30 fleet will be all weather airdrop capable. C-130Js will be delivered as weather (WC), electronic combat (EC), and tanker (KC) configured aircraft.The United States Marine Corps has chosen the KC-130J tanker to replace its aging KC-130F tanker fleet. The new KC-130J offers increased utility and much needed improvement in mission performance. As a force multiplier, the J tanker is capable of refueling both fixed wing and rotary wing aircraft as well as conducting rapid ground refueling. The refueling speed envelope has been widened from 100 to 270 knots indicated airspeed, offering more capability and flexibility. Offload rates per refueling pod can be up to 300 gallons / 2,040 lbs (1,135 liters / 925 kg) per minute simultaneously. The J tanker's offload is significantly greater than previous Herc tankers. As an example, at 1,000 nautical miles, the fuel offload is well over 45,000 lbs. Rapid ground refueling is also a premium capability. In austere conditions/scenarios, the KC-130J can refuel helicopters, vehicles, and fuel caches at 600 gallons / 4,080 lbs (2,270 liters / 1,850 kg) per minute. Additionally, the unique prop feathering capability while the engines are still running ("HOTEL Mode") offers safer and more hospitable conditions for ground refueling than in the past.
The WC-130J Hercules is a special weather reconnaissance version of the new Lockheed Martin C-130J cargo plane. Its mission is to fly into the eye of hurricanes to retrieve critical information about active storms. The Air Force Reserve Command's 53rd Weather Reconnaissance Squadron at Keesler Air Force Base, MS, a component of the 403rd Wing, is the only unit in the Department of Defense that flies this mission.

The standard C-130J has essentially the same dimensions as the C-130E/H but the J-30 (stretched version) is 15 feet longer. The J-30 incorporates two extension plugs, one forward and one aft. The foward plug is 100 inches long while the rear plug is 80 inches for a total of 180 inches or 15 feet. With its 3,000 nautical mile range, increased speed, and air refueling capability, it complements the C-5/C-17 airlift team. The J-30 can work in the strategic, as well as tactical or intratheater, environment. The J-30 can be an effective force multiplier in executing the US Army Strategic Brigade Airdrop (SBA). The J-30 can airdrop 100% of the SBA requirement. No longer is it necessary to expend scarce heavy lift resources on strategic contingency requirements. Whether it's a channel, special airlift, training, or contingency airdrop mission, the J-30 can handle it all at a significantly reduced cost.
For the first time in the 40-plus year history of the popular Hercules transport, the US Air Force and Lockheed Martin Aeronautical Systems signed a commercial practices contract for the sale of C-130Js. Awarded on 06 November 1996, the basic contract includes an initial order for two aircraft, associated data, and spares, funded in fiscal year 1996. The contract also contains five years of options through the year 2000 for additional aircraft, interim contractor support, data, training, and support. By late 1996 Aeronautical Systems had completed assembly of the first "production" C-130J (Serial # 5440), one of 12 ordered by the Royal Australian Air Force.
Design Features
In its personnel carrier role, the C-130 can accommodate 92 combat troops or 64 fully equipped paratroops on side-facing seats. For medical evacuations, it carries 74 litter patients and two medical attendants. Paratroopers exit the aircraft through two doors on either side of the aircraft behind the landing-gear fairings. Another exit is off the rear ramp for airdrops.The C-130 can deliver personnel, equipment or supplies either by landing or by various aerial delivery modes. Three primary methods of aerial delivery are used for equipment.
- In the first, parachutes pull the load, weighing up to 42,000 pounds, from the aircraft. When the load is clear of the plane, cargo parachutes inflate and lower the load to the ground.
- The second method, called the Container Delivery System, uses the force of gravity to pull from one to 16 bundles of supplies from the aircraft. When the bundles, weighing up to 2,200 pounds each, are out of the aircraft, parachutes inflate and lower them to the ground.
- The Low Altitude Parachute Extraction System is the third aerial delivery method. With LAPES, up to 38,000 pounds of cargo is pulled from the aircraft by large, inflated cargo parachutes while the aircraft is five to 10 feet above the ground. The load then slides to a stop within a very short distance. Efforts are underway to increase the maximum load weights for LAPES aerial delivery to 42,000 pounds.
FUSELAGE: The fuselage is a semimonocoque design and divided into a flight station and a cargo compartment. Seating is provided for each flight station. The cargo compartment is approximately 41 feet long, 9 feet high, and 10 feet wide. Loading is from the rear of the fuselage. Both the flight station and the cargo compartment can be pressurized to maintain a cabin pressure-altitude of 5000 feet at an aircraft altitude of 28,000 feet.
WINGS: The full cantilever wing contains four integral main fuel tanks and two bladder-type auxiliary tanks. Two external tanks are mounted under the wings. This gives the C-l 30 a total usable fuel capacity of approximately 9680 U.S. gallons.
EMPENNAGE: A horizontal stabilizer, vertical stabilizer, elevator, rudder, trim tabs, and a tail cone make up the empennage. This section consists of an all-metal full cantilever semimonocoque structure. It is bolted to the aft fuselage section.
POWER PLANT: (prior to the C-130J) Four Allison turboprop engines are attached to the wings. The engine nacelles have cowl panels and access doors forward of a vertical firewall. Clam-shell doors are located aft of the vertical firewall. Air enters the engine through a scoop assembly at the front of the nacelle.
PROPELLERS: (prior to the C-130J) Four Hamiliton Standard electro-hydromatic, constant-speed, full feathering, reversible-pitch propellers are installed on each engine.
LANDING GEAR AND BRAKES: The modified tricycle-type landing gear consists of dual nose gear wheels and tandem mains. Main gear retraction is vertically, into fuselage fairings, and the nose gear folds forward into the fuselage. Power steering is incorporated into the nose gear. The landing gear design permits aircraft operation from rough, unimproved runways. The brakes are hydraulically operated, multiple-disc type. The braking system incorporates differential braking and parking brake control. A modulating anti-skid system is provided.
AUXILIARY POWER UNIT (APU) (C-130H): The APU supplies air during ground operation for engine starting and air conditioning. One 40 KVA AC generator is mounted on the APU as an additional AC power source. Emergency electrical power during flight is also available up to 20,000 feet.
GAS TURBINE COMPRESSOR (GTC) AND AIR TURBINE MOTOR (ATM) (C-130E): C-13OE model aircraft have a GTC which supplies bleed air for engine start, air conditioning, and operation of an ATM. The ATM powers a 20 KVA electrical generator to supply auxiliary electrical power on the ground only.
OIL: The C-130 has four independent oil systems with a 12 gallon capacity for each engine. Oil is serviced through a filler neck located on the upper right engine cowling.
FUEL: The fuel system consists of a modified manifold-flow type incorporating fuel crossfeed, single point refueling (SPR) and defueling, and fuel dumping. Latest USAF versions incorporate blue foam for fire suppression.
ELECTRICAL: AC electrical power for the C-130H model is provided by five 40 KVA generators, 4 driven by the engines and one driven by the APU. On the E model, the power is supplied by four 40 KVA engine-driven generators, and a 20 KVA generator driven by the ATM. DC power is provided from AC sources through four 200 ampere transfomer rectifiers and one 24 volt, 36 ampere-hour battery.
HYDRAULIC: Four engine-driven pumps supply 3000 psi pressure to the utility and booster systems. An electric AC motor-driven pump supplies pressure to the auxiliary system and is backed up by a handpump. The hydraulic system maintains constant pressure during zero or negative "g" maneuvers.
AIR CONDITIONING AND PRESSURIZATION: Two independent air conditioning systems for the flight deck and cargo compartment are operated from engine bleed air in flight and by the GTC/APU on the ground.
OXYGEN: Both models have a 25 liter liquid oxygen (LOX) type system which provides for 96 man-hours of oxygen at 25,000 feet. It uses diluter-demand automatic pressure-breathing regulators. Portable units are also provided. System pressure is maintained at 300 psi.
FLIGHT CONTROLS: The primary flight control system consists of conventional aileron, elevator, and rudder systems. Hydraulic power boost is incorporated in each system.
WING FLAPS: The wing flaps are high-lift, Lockheed-Fowler type and are of conventional design and construction. Normal operation is by hydraulic motor. Emergency operation is by manual crank.
ANTI-ICING: Engine bleed air is used for anti-icing the wing and empennage leading edges, the radome, (radome anti-icing may be removed in some models, check with aircraft forms) and engine inlet air ducts. Electrical heat provides anti-icing for the propellers, windshield, and pitot tubes.
AIRCRAFT DIMENSIONS:
![]() |
Wing Span:Length: Height: Horizontal Stabilizer: |
132 feet 7 inches97 feet
9 inches 38 feet 5 inches 52 feet 8 inches |

Model | First Delivery | Last Delivery |
---|---|---|
C-130A | 1956 | Nov 1959 |
C-130B | 1959 | Mar 1963 |
C-130E | 1962 | Mar 1974 |
C-130H | 1964 | In Production |
C-130H2 | 1978 | 1992 |
C-130H3 | 1992 | 1997 |
C-130J | 1996 | In Production |
L-100 | 1964 | Dec 1968 |
L-100-20 | 1968 | Mar 1981 |
L-100-30 | 1970 | In Production |
C-130H-30 | 1980 | 1997 |
Service Life
Although service life computations are not used to determine grounding or airframe restrictions, the Air Force does use service life estimates as a planning tool to anticipate when major aircraft structural events can be expected. A key issue is the structural service life of the C-130 airframes, which depends on mission severity, fatigue, and corrosion factors.A severity factor accounts for the difference between normal civilian flying and military flying (low level, shortfield landings, etc.). Mission profile determines the severity factor, which is averaged over the aircraft's most recent two year history. This translates airframe clock hours into equivalent airframe damage hours which indicate the higher aging rate of the military airframes. On average, Active C-130 aircraft fly approximately 600 hours per year, while ARC C-130E and C-130H aircraft fly about 375 hours and 450 hours per year, respectively.
Currently, the critical fatigue component for the C-130 fleet is the center wing box, which is structurally more susceptible to the stresses of mission profile and payload. The center wing box has a limit of 60,000 relative baseline hours (flight hours multiplied by the mission severity factor).) A corrosion limit of 40,000 flight hours is based on historical data and engineering judgment. It considers corrosion factors not considered in airframe fatigue analysis. Actual airframe service life depends on which limit, fatigue or corrosion, is reached first.
The average age of the active duty C-130 fleet is over 25 years old, while the average age of Guard and Reserve C-130s is 15 years old. The average age of the C-130E model is over 28 years and average flying time is approximately 19,800 hours; the newest E-model being produced in 1972. Based on projected operations tempo and overall mission severity, C-130E aircraft have an average remaining service life of 15 years. Material solutions such as selective repair, a service life extension program (SLEP), or procurement of new aircraft are several ways to influence and resolve aging of the C-130 fleet.
The service-life of the HC-130N/P is based upon the aircraft�s wing box and operations tempo. Based on the current operations tempo, the fleet will begin to lose airworthiness in 2013.
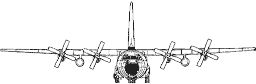
Specifications | |
Primary Function | Intratheater airlift. |
Contractor | Lockheed Aeronautical Systems Company. |
Power Plant | Four Allison T56-A-15 turboprops; 4,300 horsepower, each engine. |
Length | 97 feet, 9 inches (29.3 meters). |
Height | 38 feet, 3 inches (11.4 meters). |
Wingspan | 132 feet, 7 inches (39.7 meters). |
Speed | 374 mph (Mach 0.57) at 20,000 feet (6,060 meters). |
Ceiling | 33,000 feet (10,000 meters) with 100,000 pounds (45,000 kilograms) payload. |
Maximum Takeoff Weight | 155,000 pounds (69,750 kilograms). |
Operating Weight: | 83,000 Pounds |
Maximum Useable Fuel: | 60,000 Pounds |
Maximum Allowable Cabin Load: | 36,000 Pounds |
Normal Passenger Seats Available: | Up to 92 troops or 64 paratroops or 74 litter patients. |
Maximum Number of Pallets: | 5 |
Range | 2,356 miles (2,049 nautical miles) with maximum payload; 2,500 miles (2,174 nautical miles) with 25,000 pounds (11,250 kilograms) cargo; 5,200 miles (4,522 nautical miles) with no cargo. |
Unit Cost | $22.9 million (1992 dollars). |
Crew | Five (two pilots, a navigator, flight engineer and loadmaster); up to 92 troops or 64 paratroops or 74 litter patients or five standard freight pallets. |
Minimum Crew Complement | Four (two pilots, one flight engineer, and one loadmaster) Allows for a 16 hour crew duty day (12 hour for airdrop crews) (from show at the aircraft to parking at the final destination). |
Crew Complement [airdrop missions] |
Six crews will normally carry one navigator as well and an extra loadmaster in addition to the minimum crew complement. |
Augmented Crew Complement | Nine (three pilots, two navigators, two flight engineers, and two loadmasters) Allows for a 18 hour crew duty day (from show at the aircraft to parking at the final destination) |
Date Deployed | April 1955. |
Inventory | Active force, 98; ANG, 20 Bs, 60 E's and 93 H's; Reserve, 606. |
The most significant issue for the C-130 entails the reassignment of CONUS-based active duty C-130s from USACOM to USTRANSCOM. As the single manage for DoD transportation, the consolidation of these air mobility assets under USTRANSCOM lends further credence to USTRANSCOM�s single manager charter. Furthermore, as the Air Force component of USTRANSCOM, AMC now exercises both service authority (i.e., train, organize, equip, and provide) and operational control over these forces. This arrangement eliminates confusion and yields more effective and efficient service to the air mobility customer. (Theater CINCs will continue to exercise combatant command and operational control of overseas-assigned C-130 forces.)
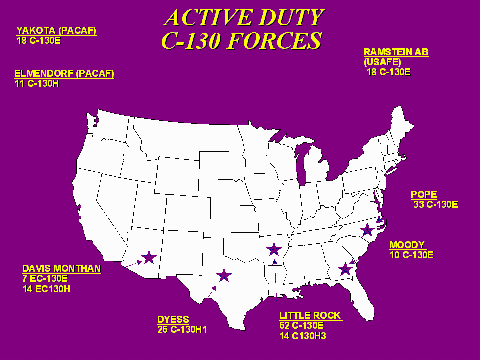
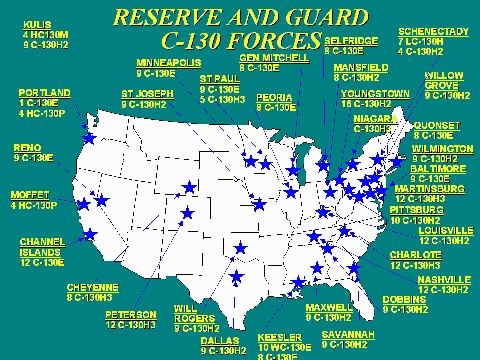
VRML 3-D Model |
![]() C-130 Hercules VRML by Soji Yamakawa |

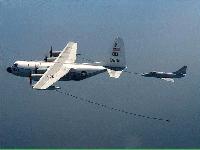
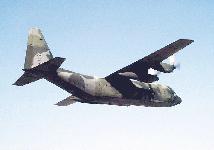
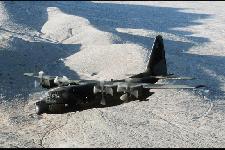
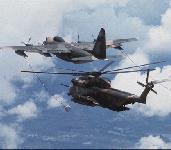
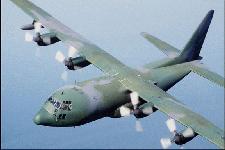
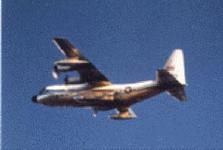

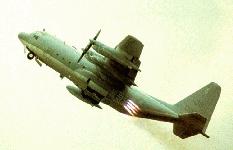
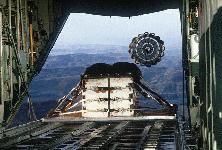
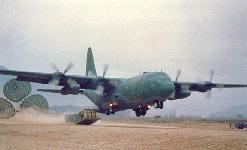
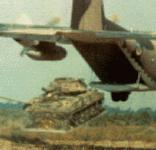
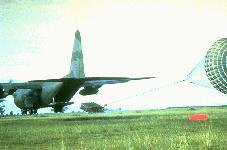

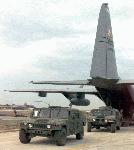
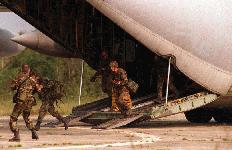
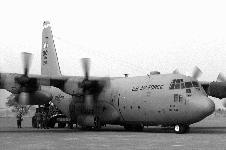
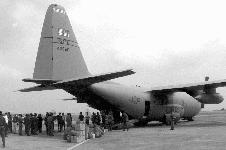
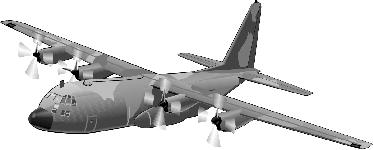
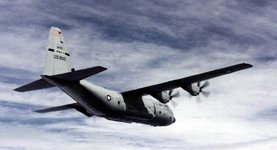
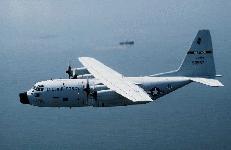
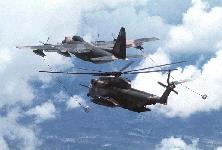
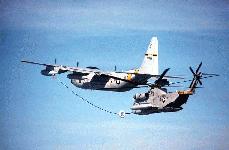
No comments:
Post a Comment