Sudipta Chakraborty is the
Director of Energy Systems at OPAL-RT. In this Engineer Spotlight, Dr.
Chakraborty speaks about challenges facing power system design, how
hardware-in-the-loop simulations are important for problem-solving with
grid integration, and his work on the IEEE-1547 standard for power grid
test procedures.
The work of Dr. Sudipta Chakraborty, Director of Energy Systems at OPAL-RT, is looking to foster these changes by focusing on developing real-time simulation technology for power systems, as well as automotive, robotics, aerospace, and other applications.
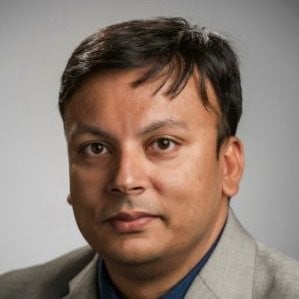
Dr. Sudipta Chakraborty
Dr. Chakraborty is using his experience and expertise as a technical leader, engineer, designer, and researcher to bridge the gaps between industry, research laboratories, and academia. Over the years, has innovated the use of hardware-in-the-loop for power systems applications, chaired the IEEE 1547 standard committee (which outlines test procedures for power grids), and worked on grid integration of renewable and distributed energy sources.
Currently, Dr. Chakraborty is working at OPAL-RT with an aim to help power systems and power electronics engineers by providing real-time simulation and hardware-in-the-loop tools. His goal is to help these engineers make better designs that are more efficient and provide improved power system-level performance at reduced cost.
“Hardware-in-the-loop can answer big questions in power systems, power electronics, and grid integrations of renewable energy which are all important research fields. As I see more and more system-level needs increasing for energy applications, I think hardware-in-the-loop is one of the fields that everybody is now looking into to solve these research challenges.”All About Circuits writer, Chantelle Dubois, recently had a chance to talk to Dr. Chakraborty about his fascinating career and what his thoughts are on the future of energy systems and renewable energy.
Chantelle Dubois (AAC): Tell us a bit about yourself. What's your career been like so far that brought you to OPAL-RT?
Dr. Sudipta Chakraborty (SC): I completed my Bachelors in Electrical Engineering in India and then I came to the US to the Colorado School of Mines to do my Ph.D. on power systems and power electronics. I was working on power electronics and power system applications for a renewable and grid integration. I graduated from the Colorado School of Mines in 2007.
After that, I joined the National Renewable Energy Laboratory (NREL), a US Department of Energy national lab, as a post-doctoral researcher in 2007. At NREL, I started working on a similar topic, 'Grid Integration of Renewable and Distributed Energy,' mainly focusing on power electronics, which is the power conversion needed for converting a renewable energy to an energy that you can use. I started as post-doc, then I became an engineer, then a senior engineer. At one point, I was actually leading a Power Electronics and Controls section at NREL.
Then, finally, I became a principal engineer, which, at that time, was the second-highest engineering level position at that time. I was at NREL for 10 years, from 2007 to 2017, working on grid integration, how to add more renewable energy for the grid, [dealing with issues like] how can you make them operate safely with the current electric grid structure.
I was with NREL until last July. I then came across OPAL-RT and I was interested in bringing my experience and expertise [in academia to help industry], bridging that gap.
AAC: What's OPAL-RT's background?
SC: It started 20 years back, founded by Jean Belanger, current President and CTO. And it come from an idea: How can we make a real-time simulation tool and put it in the hands of the common researcher? Not everybody will have a supercomputer in their lab for applications like photovoltaic system design.
How can you make these things cheaper? How you can give them to the common researcher to solve the research problems which are very challenging and which are not easy to solve without the help of such tools? Without these tools, it will be all trial-and-error.
AAC: What inspired you to get into the field that you're in? It sounds like you started in power electronics and then branched out into renewable energy and real-time simulations.
SC: Yes, exactly. Power electronics, power systems—as I said, those are broad categories. So, you have electrical engineering: a very broad category. And then there are different research topics, one of those related to power systems. And, under power systems, there are various subtopics, like power electronics, controls, operations, planning, etc.
My initial training was to build the power electronics systems for grid integration from scratch and then I quickly realized—yes, it's good to build one of those systems and show they work. But, at the end of the day, you need to make sure they work very well when you put them into a bigger, larger power system like an electric grid. Utility companies have concerns about grid reliability, so they don't want things to be put into their grid that can create problems into their systems.
So, as a researcher, I started getting more interested in how you could validate or look into system-level interaction of power devices. Around 2009-2010 [while at NREL], I came across this new technology called 'hardware-in-the-loop' or HIL. Hardware-in-the-loop is not a new technology—in other industries, like aerospace space applications, they use hardware-in-the-loop testing since they cannot test their systems on a real airplane or in real space flight. That would be billions of dollars' worth of problems. But it was not, I would say, that common for the electrical engineering field in terms of how you validate or how you test things. So we started looking into how you could create a flight simulator for power systems.
So, here's how I put it. How can you create a flight simulator where you don't really need to run an airplane but you can have a model of the airplane and then you can test some other things with that airplane, without actually destroying the actual hardware or the actual costly systems. That's the motivation that got me into hardware-in-the-loop simulation, [which has become] more and more popular.
Hardware-in-the-loop can answer big questions in power systems, power electronics, and grid integrations of renewable energy, which are all large research fields. So, that is the main motivation for me. I am still a power electronics engineer by training. I know power electronics controls very well. I can develop inverters. But as I see more and more system-level needs increasing, I think hardware-in-the-loop is one of the fields that I think everybody is now looking into to solve those problems.
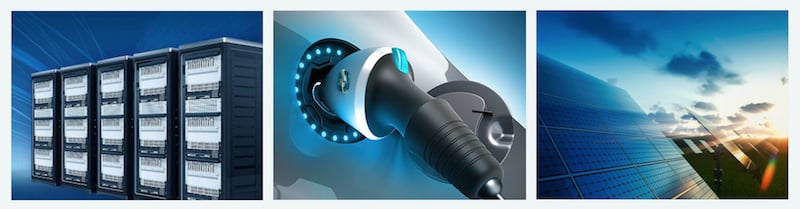
OPAL-RT considers modular multi-level converters (MMC), hybrid and electrical transportation, and energy conversion controls to be its top three power electronics applications.
AAC: What kind of problems does hardware-in-the-loop solve with power systems?
SC: There are several system-level questions that can be addressed. For example, grid integration of renewable energy: What happens when you have high penetration of those inverter-based renewable energy systems in your grid?
Another example is that there are lots of micro-grids around you nowadays, so how do you validate a micro-grid that consists of a number of sources and loads? Do you want to go to the field and do a million dollar experiment to do that? Or is there any other way that you can validate the controls and some of the operations before you go to the field?
A third example that is more common is how you can look into the cybersecurity aspect of a grid. So it is not just the electrical system anymore—it also has communications and the interaction of the communications with the actual power devices.
Hardware-in-the-loop allows you to run models of systems (such as power systems or power converters) with real components (such as controllers or sensors) together and create some of the conditions that those components will experience in real life.
In some applications, you can even test a power systems component, such as an inverter with a simulated power systems model. For example, you can use these hardware-in-the-loop techniques to test a photovoltaic (PV) inverter that you will see in real life without actually putting it in the real distribution feeder. You can simulate the rest of the power systems in our real-time platform and then, using power amplifiers, you can test how that PV inverter will behave if you put it in real-world conditions and see how it will impact the whole power system.
AAC: Tell us a bit about your involvement with the IEEE-1547 standard committee. What has that work been like?
SC: You can think of IEEE-1547 as more or less the standard that anybody or everybody has to use in the US when they have to connect distributed energy resources (DERs) to the electric grid. IEEE-1547 was developed to address the need to standardize the interconnection of these DERs to the electric grid.
For example, if someone is connecting a PV inverter, how will the electric utility know that the inverter is compatible with the rest of the system? Is it safe? Is it going to last for five years? Ten years? You don't know. And how's that's going to work?
Before 2002-2003, there was no specific way you could test those devices. So, that's the reason for this particular standard which is the "IEEE Standard for Interconnection and Interoperability of Distributed Energy Resources with Associated Electric Power Systems Interfaces".
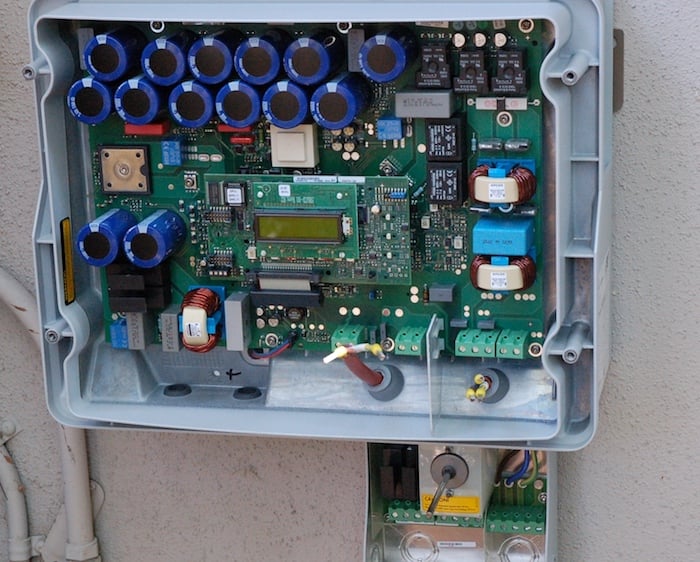
An example of a solar converter. Image courtesy of Russell Neches [CC BY 2.0].
The work on IEEE-1547 started around the year 2000, published in 2003, and it became very successful in terms of coming up with a standard that could be trusted and works reliably. When you connect a photovoltaic inverter in your home, initially, there was no certification, which was actually hindering some of the growth of the photovoltaic industry.
The standards working group also developed a test procedure for this standard, which is IEEE 1547.1, published around 2005, for power electronics, power converters, and devices for DERs. Later, UL adopted those test procedures as a part of their standards which is called UL-1741.
As we now have significantly higher DERs in the grid, IEEE 1547 and 1547.1 needed major revisions. So, my work at NREL was to support the revision of IEEE-1547 based on our experience, our expertise, what's needed for the future grid. That work was recently concluded and the revised standard was published this month.
One of the roles I was also doing before I joined OPAL-RT was to help in the testing of DERs. If you have an inverter, for example, how are you going to test it so you know it will comply with the revised IEEE-1547? Before I left NREL, I was the chair for the IEEE-1547.1 revision working group. One of my colleagues is now leading it, although I am still very involved and I am very proud of that involvement.
At NREL, I was also involved in several other IEEE standards in parallel, like some of the micro-grid-related standards. These standards will help with grid stability, allow it to accept more renewable energy, and enable additional functions that are not available as of today.
These standards will help with grid stability, allow it to accept more renewable energy, and enable additional functions that are not available as of today.
On the OPAL-RT side, we are very involved in terms of how we can test these devices with new functionalities using new techniques such as hardware-in-the-loop. Suppose you're developing a new inverter with these new functions. How are we going to do the product development and test those products in an efficient way? Because you cannot just go to a certification testing and expect everything is going to work in the first trial. And the certification process is costly. So, many inverter manufacturers have some of the hardware-in-the-loop tools in-house—as well as some of the research labs used HIL—to validate those kinds of things before they go into either a field demonstration or a certification.
So, we're playing a part there. Our part is to support product development and validation and to make those products more robust before they are put into the field. So, that's my relation to standards-related activities nowadays because I'm not actively running those—but I want to still learn about the new products that are coming out and develop ideas on how we can contribute to make this whole process, whole ecosystem, work better.
AAC: Your work at OPAL-RT brings all of your expertise and experience together through better simulation systems. Why is this important for the industry?
SC: I said we talk about all the system challenges, we talk about components, we talk about renewable energy—all kinds of things. But, at the bottom line is that you need to have a better product. You need to have a better system. You need to have new controls and algorithms. Those things have to be validated before you do a costly demonstration or testing.
OPAL-RT has different platforms. We have different types of simulation, real-time simulation hardware platforms. And the biggest thing we provide starts from a small, device-level scale.
Suppose you are a power electronics engineer developing a new system, like a new converter that converts one form of electricity to another. This involves different things. It involves a switch. It involves some protection. It involves a control. So, you have your control algorithms to make whole things work. And how you do that? In the olden days, when I was in grad school, I used to do just the simulation. And I said, "okay, the simulation is good. Now, I'll build it in my hardware and I hope I translate what I did in my simulation properly into my actual controller, in the hardware, and I hope it will work."
On the OPAL-RT side, we have a couple of tools. One, we call eFPGASIM, which is for FPGA simulation, and the other one is called eMEGASIM, which is our EMT (electromagnetic transient) simulation. These tools allow the manufacturer or researcher who is working on control algorithms and things on a smaller scale, like a component, to actually develop their controls first in simulation. They can then [proceed to] build their controller on their hardware.
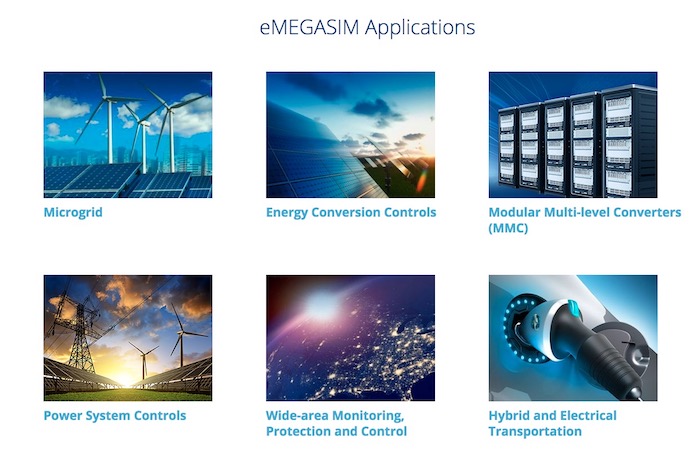
We're actually now testing the actual controller board through this method we call controller-hardware-in-the-loop, where the controller is connected to a simulated inverter behaving the same way as a real inverter. This mitigates a lot of risk out of product development through algorithm development controls.
OPAL-RT also provides the tools that actually can model the power systems, either in the electromagnetic transient domain or in your phasor domain, which is another scale. These are all different timescales, different types of applications—each has their own application.
Bottom line here is that our tools can be used as an integrated platform. You can now connect that converter that you developed or even the controller board that you developed up to a system-level simulation of the electric grid. And remember I was talking about how multiple inverters will work? How will multiple controls work? You can address those questions easily because now you don't have to connect them to a real electric system but you can still look into their system-level behavior.
So, I mentioned control-hardware-in-the-loop. And then the next step comes as a power-hardware-in-the-loop. In that case, suppose you have a commercial inverter. Or you build your own inverter and have tested it at power but then you want to replicate rest of the system in your simulation. Then you can see how that real inverter will behave with a simulated distribution feeder and that will give you an idea, like how that will behave in the field, when instead of the simulated distribution feeder, you have a read distribution feeder.
We are providing tools and systems to our customers, who are then using them for their own research challenges. But we also have to evolve because the research challenges change, which influences our own R&D to improve our tools or add some capabilities to our tools to help those researchers.
No comments:
Post a Comment