The PLC or Programmable Logic Controller has revolutionized the
automation industry. Today PLCs can be found in everything from factory
equipment to vending machines, but prior to New Year’s Day 1968 the
programmable controller didn’t even exist. Instead what existed was a
unique set of challenges that needed a solution. In order to understand
the history of the PLC we must first take some time to understand the
problems that existed before programmable controllers.
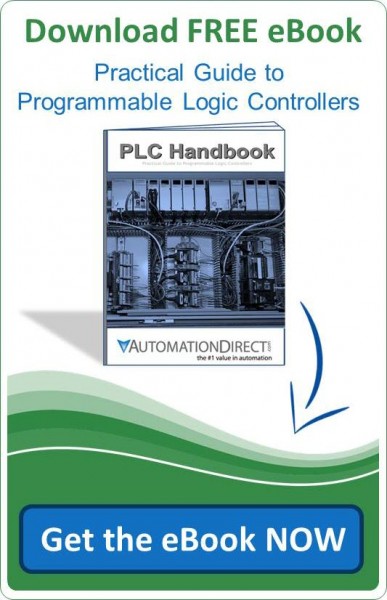
Think about modern factories, and how many motors and ON/OFF power switches you would need to control just one machine. Then add on all the control relays you need and what you get is… Yes, machine control, but you also get a logistical nightmare. All these relays had to be hardwired in a very specific order for the machine to work properly, and heaven forbid if one relay would have an issue, the system as a whole would not work.
Troubleshooting would take hours, and because coils would fail and contacts would wear out, there was need for lots of troubleshooting. These machines had to follow a strict maintenance schedule and they took up a lot of space. Then what if you wanted to change something? You would basically have to redo the entire system. It soon became clear that there were problems installing and maintaining these large relay control systems.
Let’s hear from a controls designer in the thick of things in the early ‘70s –
“Upon graduating from technical college in 1970, I began working as a controls designer, automating metal working machinery and equipment with industrial relays, pneumatic plunger timers, and electro-mechanical counters. Also included were fuses, control transformers, motor starters, overload relays, pushbuttons, selector switches, limit switches, rotary drum sequencers, pilot lights, solenoid valves, etc.
The relay based control systems I created included anywhere from 50 to well over 100 relays. The electrical enclosures to house the controls would typically be six feet wide by four feet high, mounted near the machinery. Picture lots of wires bundled and laced together, connecting the relays, timers, counters, terminals, and other components, all nice and tidy. Then picture after a few months or years the same wiring, after many engineering changes and troubleshooting, being out of the wire duct or unlaced; in many cases wires were added in a crisscross, point-to-point pattern to take the shortest route and amount of time to make the change. We referred to the condition of these control enclosures as a rat’s nest; reliability suffered, along with an increase in difficulty during troubleshooting, or making additional operational engineering changes.”
The popular forum PLCDEV.com outlines a list of requirements that GM engineers put out for a “standard machine controller.” It is this request that Dick Morley and his company, Bedford and Associates, were responding to when the first PLC was envisioned. Besides replacing the relay system, the requirements listed by GM for this controller included:
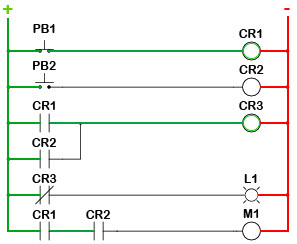
The programming look of the PLC required that it be easily understood and used by maintenance electricians and plant engineers. As relay-based control systems evolved and became more complicated, the use of physical component location wiring diagrams also evolved into the relay logic being shown in a ladder fashion. The control power hot wire would be the left rail, with the control power neutral as the right rail. The various relay contacts, pushbuttons, selector switches, limit switches, relay coils, motor starter coils, solenoid valves, etc., shown in their logical order would form the ladder’s rungs. It was requested that the PLC be programmed in this Ladder Logic fashion.
As Dick Morley laments in his memoirs, the process from idea to actual controller wasn’t all smooth sailing.
Eventually Dick Morely spun off a new company named Modicon and started to sell those first PLCs, the Modicon 084 (named because it was prototype #84). It was the Modicon 084 that was presented to GM to meet its criteria for its “standard machine controller.” Modicon started to sell the 084 with very limited success. As Dick Morley puts it, “Our sales in the first four years were abysmal.” But nevertheless the company continued to learn and develop. Eventually, Modicon would bring to life the controller that would change the industry forever, the Modicon 184. Dick Morley writes this about the 184:
“The thing that made the Modicon Company and the programmable controller really take off was not the 084, but the 184. The 184 was done in design cycle by Michael Greenberg, one of the best engineers I have ever met. He, and Lee Rousseau, president and marketer, came up with a specification and a design that revolutionized the automation business. They built the 184 over the objections of yours truly. I was a purist and felt that all those bells and whistles and stuff weren’t “pure”, and somehow they were contaminating my “glorious design”, Dead wrong again, Morley! They were specifically right on! The 184 was a walloping success, and it—not the 084, not the invention of the programmable controller—but a product designed to meet the needs of the marketplace and the customer, called the 184, took off and made Modicon and the programmable controller the company and industry it is today.”
Image Courtesy of RepairZone.com
As the functionality of the Porgrammable Logic Controller evolved, programming devices and communications also saw rapid growth. The first programming devices were dedicated, but unfortunately the size of suitcases. Later, handheld programming devices came into the picture, but soon were replaced with proprietary programming software running on a personal computer. AutomationDirect’s DirectSOFT, developed by Host Engineering, was the first Windows-based PLC programming software package.
Having a PC communicating with a PLC provided the ability to not only program, but also allowed easier testing and troubleshooting. Communications started with the MODBUS protocol using RS-232 serial communications. The addition of various automation protocols communicating over RS-485, DeviceNet, Profibus, and other serial communication architectures have followed. The use of serial communications and the various PLC protocols also allowed PLCs to be networked with other PLCs, motor drives, and human to machine interfaces (HMI). Most recently EtherNet and protocols such as EtherNet/IP (for Industrial Protocol) have gained tremendous popularity.
Before the Programmable Controller
Before the days of the PLC the only way to control machinery was through the use of relays. Relays work by utilizing a coil that, when energized, creates a magnetic force to effectively pull a switch to the ON or OFF position. When the relay is de-energized, the switch releases and returns the device to its standard ON or OFF position. So, for example, if I wanted to control whether a motor was ON or OFF, I could attach a relay between the power source and the motor. Then I could control when the motor is getting power by either energizing or de-energizing the relay. Without power, of course, the motor would not run, thus I am controlling the motor. This type of relay is known as a power relay. There could be several motors in one factory that need to be controlled, so what do you do? You add lots of power relays. So factories started to amass electrical cabinets full of power relays. But wait, what switches the coils in the power relays ON and OFF before the power relay turns the motor ON, and what if I want to control that? What do you do? More relays. These relays are known as control relays because they control the relays that control the switch that turns the motor ON and OFF. I could keep going, but I think you get the picture of how machines were controlled pre-PLC, and, more importantly, I think you start to see some of the problems with this system of electromechanical control via relays.![Signalhead at the English language Wikipedia [GFDL (http://www.gnu.org/copyleft/fdl.html) or CC-BY-SA-3.0 (http://creativecommons.org/licenses/by-sa/3.0/)], via Wikimedia Commons History of PLC](https://upload.wikimedia.org/wikipedia/commons/thumb/b/be/Relay_room.jpg/512px-Relay_room.jpg)
Courtesy of Signalhead via Wikimedia Commons
The Problem with Relays
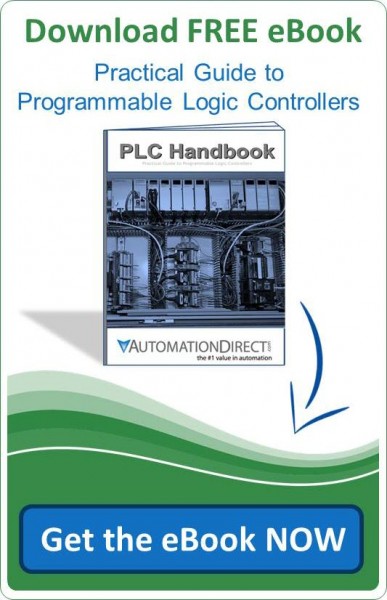
Think about modern factories, and how many motors and ON/OFF power switches you would need to control just one machine. Then add on all the control relays you need and what you get is… Yes, machine control, but you also get a logistical nightmare. All these relays had to be hardwired in a very specific order for the machine to work properly, and heaven forbid if one relay would have an issue, the system as a whole would not work.
Troubleshooting would take hours, and because coils would fail and contacts would wear out, there was need for lots of troubleshooting. These machines had to follow a strict maintenance schedule and they took up a lot of space. Then what if you wanted to change something? You would basically have to redo the entire system. It soon became clear that there were problems installing and maintaining these large relay control systems.
Let’s hear from a controls designer in the thick of things in the early ‘70s –
“Upon graduating from technical college in 1970, I began working as a controls designer, automating metal working machinery and equipment with industrial relays, pneumatic plunger timers, and electro-mechanical counters. Also included were fuses, control transformers, motor starters, overload relays, pushbuttons, selector switches, limit switches, rotary drum sequencers, pilot lights, solenoid valves, etc.
The relay based control systems I created included anywhere from 50 to well over 100 relays. The electrical enclosures to house the controls would typically be six feet wide by four feet high, mounted near the machinery. Picture lots of wires bundled and laced together, connecting the relays, timers, counters, terminals, and other components, all nice and tidy. Then picture after a few months or years the same wiring, after many engineering changes and troubleshooting, being out of the wire duct or unlaced; in many cases wires were added in a crisscross, point-to-point pattern to take the shortest route and amount of time to make the change. We referred to the condition of these control enclosures as a rat’s nest; reliability suffered, along with an increase in difficulty during troubleshooting, or making additional operational engineering changes.”
– Tom, Controls Designer
Birth of the PLC Solution
So what was the solution? I am sure this is the exact question that engineers at the Hydra-Matic division of General Motors were struggling with every day. Fortunately, at that time, the concept of computer control had started to make its way into conversations at large corporations such as GM. According to Dick Morley, the undisputed father of the PLC, “The programmable controller was detailed on New Year’s Day, 1968.”The popular forum PLCDEV.com outlines a list of requirements that GM engineers put out for a “standard machine controller.” It is this request that Dick Morley and his company, Bedford and Associates, were responding to when the first PLC was envisioned. Besides replacing the relay system, the requirements listed by GM for this controller included:
- A solid-state system that was flexible like a computer but priced competitively with a like kind relay logic system.
- Easily maintained and programmed in line with the already accepted relay ladder logic way of doing things.
- It had to work in an industrial environment with all its dirt, moisture, electromagnetism and vibration.
- It had to be modular in form to allow for easy exchange of components and expandability.
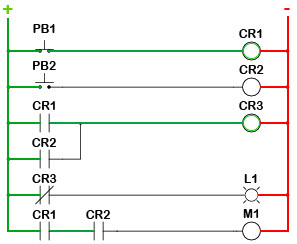
The programming look of the PLC required that it be easily understood and used by maintenance electricians and plant engineers. As relay-based control systems evolved and became more complicated, the use of physical component location wiring diagrams also evolved into the relay logic being shown in a ladder fashion. The control power hot wire would be the left rail, with the control power neutral as the right rail. The various relay contacts, pushbuttons, selector switches, limit switches, relay coils, motor starter coils, solenoid valves, etc., shown in their logical order would form the ladder’s rungs. It was requested that the PLC be programmed in this Ladder Logic fashion.
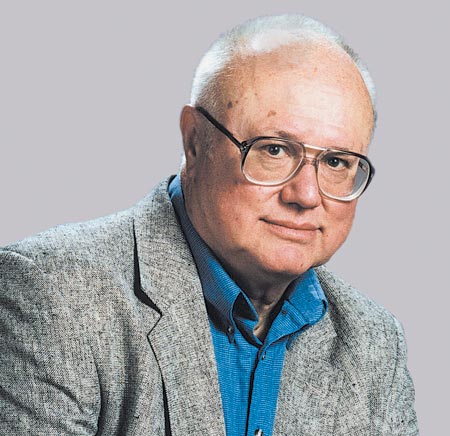
Image of Dick Morley
Courtesy of AutomationWorld.com
“The initial machine, which was never delivered, only had 125 words of memory, and speed was not a criteria as mentioned earlier. You can imagine what happened! First, we immediately ran out of memory, and second, the machine was much too slow to perform any function anywhere near the relay response time. Relay response times exist on the order of 1/60th of a second, and the topology formed by many cabinets full of relays transformed to code is significantly more than 125 words. We expanded the memory to 1K and thence to 4K. At 4K, it stood the test of time for quite a while.”Tom, our controls designer, recounts, “My experience in creating relay-based control systems, at that time, put me in the perfect position to be one of the first control system designers to use some of the very first programmable controllers to replace relay-based control systems. My first experience with a PLC happened to be with one of Bedford Associates competitor’s solid state devices. The unit was programmed with a suitcase-sized programming device that required setting the instruction type and line address and then pressing a button to burn a fuse link open in a memory chip to set the logic path. Once the programming was completed and tested, the PLC was able to perform the machine cycle operation in a very reliable manner. Unfortunately the PLC card rack was open in the rear with a mixture of 24 VDC and 120 VAC power and signals. It didn’t take much for an electrician checking signals during troubleshooting to accidently short the 120 VAC to the 24 VDC and take out the entire PLC system. Being the first use of a PLC in a large corporation, the failure doomed the use of PLCs at this manufacturing facility for a couple of years.”
Eventually Dick Morely spun off a new company named Modicon and started to sell those first PLCs, the Modicon 084 (named because it was prototype #84). It was the Modicon 084 that was presented to GM to meet its criteria for its “standard machine controller.” Modicon started to sell the 084 with very limited success. As Dick Morley puts it, “Our sales in the first four years were abysmal.” But nevertheless the company continued to learn and develop. Eventually, Modicon would bring to life the controller that would change the industry forever, the Modicon 184. Dick Morley writes this about the 184:
“The thing that made the Modicon Company and the programmable controller really take off was not the 084, but the 184. The 184 was done in design cycle by Michael Greenberg, one of the best engineers I have ever met. He, and Lee Rousseau, president and marketer, came up with a specification and a design that revolutionized the automation business. They built the 184 over the objections of yours truly. I was a purist and felt that all those bells and whistles and stuff weren’t “pure”, and somehow they were contaminating my “glorious design”, Dead wrong again, Morley! They were specifically right on! The 184 was a walloping success, and it—not the 084, not the invention of the programmable controller—but a product designed to meet the needs of the marketplace and the customer, called the 184, took off and made Modicon and the programmable controller the company and industry it is today.”

The PLC in its teenage years
The first PLCs had the ability to work with input and output signals, relay coil/contact internal logic, timers and counters. Timers and counters made use of word size internal registers, so it wasn’t too long before simple four-function math became available. The PLC continued to evolve with the addition of one-shots, analog input and output signals, enhanced timers and counters, floating point math, drum sequencers and mathematic functions. Having built-in PID (Proportional-Integral-Derivative) functionality was a huge advantage for PLCs being used in the process industry. Common sets of instructions evolved into fill-in-the-blank data boxes that have made programming more efficient. The ability to use meaningful Tag Names in place of non-descriptive labels has allowed the end user to more clearly define their application, and the ability to import/export the Tag Names to other devices eliminates errors that result when entering information into each device by hand.As the functionality of the Porgrammable Logic Controller evolved, programming devices and communications also saw rapid growth. The first programming devices were dedicated, but unfortunately the size of suitcases. Later, handheld programming devices came into the picture, but soon were replaced with proprietary programming software running on a personal computer. AutomationDirect’s DirectSOFT, developed by Host Engineering, was the first Windows-based PLC programming software package.
Having a PC communicating with a PLC provided the ability to not only program, but also allowed easier testing and troubleshooting. Communications started with the MODBUS protocol using RS-232 serial communications. The addition of various automation protocols communicating over RS-485, DeviceNet, Profibus, and other serial communication architectures have followed. The use of serial communications and the various PLC protocols also allowed PLCs to be networked with other PLCs, motor drives, and human to machine interfaces (HMI). Most recently EtherNet and protocols such as EtherNet/IP (for Industrial Protocol) have gained tremendous popularity.
No comments:
Post a Comment