Newer cars typically feature a
tire pressure monitoring systems (TPMS) that warn drivers when a tire is
significantly under-inflated. This safety feature was deemed important
enough that the United States Department of Transportation (DOT) and the
National Highway Traffic Safety Administration (NHTSA) published a
Federal Motor Vehicle Safety Standard. Tire pressure affects a vehicle's
fuel economy, handling, and possible catastrophic tire failure. In this
application note, over-inflated detection is also included. The system
may also be used for anti-theft, warning when one of the sensors is not
sending information (in that case, one of the tires may have been
stolen).
The other system is called Indirect System. It uses the vehicle's anti-lock braking system's wheel speed sensors to compare the rotational speed of one tire versus the others. If a tire is low/high on pressure, it will roll at a different number of revolutions per kilometer than the other three and alert the vehicle's on-board computer. Indirect systems are unable to generate accurate readings in cases where all four tires are losing pressure at the same rate, such as the effects of time and temperature.
In this implementation, the Direct Tire Pressure Measurement System will be used. In this case, the pressure will be measured and analyzed locally on each tire with the SLG46620, GreenPAK configurable mixed-siganl IC (CMIC). The SLG46620 will send the information of under-pressure, over-pressure or correct pressure to the central system (onboard computer or dedicated system) via the communication system (Figure 1). With this implementation, a TPMS may also be retrofitted on older cars by adding a small central system to the console of the car.

Figure 1. Pressure measurement and Preprocessing System schematic block diagram.
Pressure Sensor
In this type of application, choosing the correct sensor is one of the most important stages in the design. An automotive application not only requires a sensor with the correct resolution and pressure range, it also requires certified sensors which are able to be used for automotive safety applications and with a low current consumption.In this case, there are two options about the type of sensor: Differential Pressure Sensors and Absolute Pressure Sensors. Differential ones measure the difference between the actual pressure and the atmosphere pressure. Absolute ones use absolute zero as its reference pressure, measured relative to a full vacuum (outer space).
Since absolute pressure uses absolute zero as a definitive reference point, absolute pressure remains precise and accurate regardless of changes in ambient or process temperature. This is the main reason for choosing Absolute Pressure Sensors
The selected pressure sensor for this application is the SM5420C-060 from SMI Pressure Sensors. It is an absolute pressure sensor with an operating pressure range of 0 to 60 PSI. The power supply must be 5V (compatible with SLG46620) and with a current low consumption of 1mA. One of the advantages of this sensor is that it is certified to be used for automotive applications, being qualified to meet AEC Q100 standards (the Automotive Electronics Council standard about Failure Mechanism based Stress Test Qualification for Integrated Circuits).
The selected pressure sensor has a differential output proportional to the measured pressure and it can be modeled as:

The output circuit can be thought as a Wheatstone bridge, as it can be seen in Figure 2.
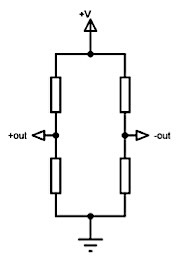
Figure 2. Output circuit – Pressure Sensor.
The most important characteristics of the sensor are shown in Table 1.
Parameter | Value |
---|---|
Power Supply | 5 V |
Input Current | 1 mA |
Operating Temperature | -40 to 125°C |
Operating Pressure | 0 to 60 PSI |
Span | 100 mV typical (135 mV max) |
Zero Offset | 0 mV |
Schematic Diagram
Due to the differential outputs of the sensor, and considering the simpler way for conditioning the signal for being acquired by SLG46620’s ADC, the external implemented circuit is shown in Figure 3.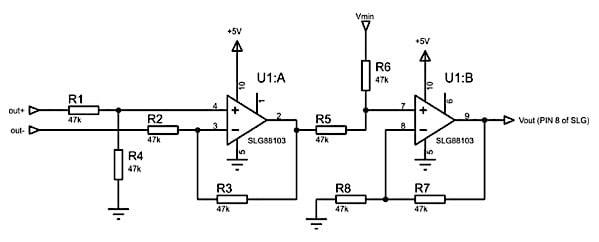
Figure 3(a). Signal conditioning schematic circuit.
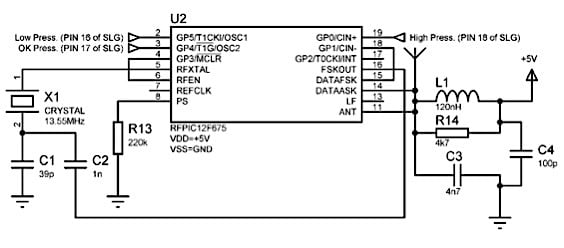
Figure 3(b). Wireless Communication System.
The signal conditioning circuit can be divided into two parts.
First of all, the differential output of the sensor (out+ and out–) is converted to a single ended signal with the operational amplifier U1. This is done by a typical differential configuration with unity gain. With this circuit, the signal obtained at the output of U1 is
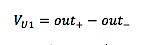
It’s important to mention that, if pressure is zero, the output voltage is zero. That’s why the operational amplifier must be a rail-to-rail operational amplifier.
The other part of the design is the second operational amplifier (U2). It is required to condition the level of the signal to meet the input specifications of the SLG46620 analog-to-digital converter.
SLG46620, in the electrical specifications of the datasheet, specifies that the ADC with the single ended configuration, must have a minimum voltage input of 30mV/G (where G is the gain of the Programmable Gain Amplifier of the ADC) to acquire the signal. To obtain this minimum level voltage, the second operational amplifier adds Vmin voltage to the single ended signal coming from the sensor and the first operational amplifier. With this configuration, the output signal (Vout) can be directly connected to the analog input of the SLG46620.
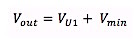
When the specifications of the ADC are considered, the maximum input level voltage in single-ended mode is 1030mv/G. If the worst case is analyzed, the maximum differential output level of the sensor can be 135mV. In this case, it can be risky if the Gain is configured to 8 (because the maximum input level is 137mV) because low pressures may not be compatible with the minimum input voltage of the ADC. For this reason, the ADC and the PGA are configured with a gain of 4. With this configuration, the maximum input level to the ADC is 274mV and the minimum input level is 7.5mV. In the case of the PGA, the linear range is between 23mV to 236mV.
With this configuration, Vmin must be between 23mV and 99mV. The selected value is 60mV, so the output range of the conditioned signal is 60mV to 195m. The Vmin voltage is obtained from the SLG46620 DAC, connecting its output to one of the GPIOs.
Implementation
As described above, the pressure measurement described in this application note is part of a car safety system. The aim of this implementation is to get benefits of the small size and low current consumption of the SLG46620, allowing to measure and process the pressure locally.Another important benefit of this implementation is the speed of processing. Considering the timing requirement of the NHTSA standard, the SLG46620 processes the sensor data very fast, so the onboard computer is free to make all the necessary verifications before reporting low or high pressure.
The GreenPAK circuit design implementation is shown in Figure 4.
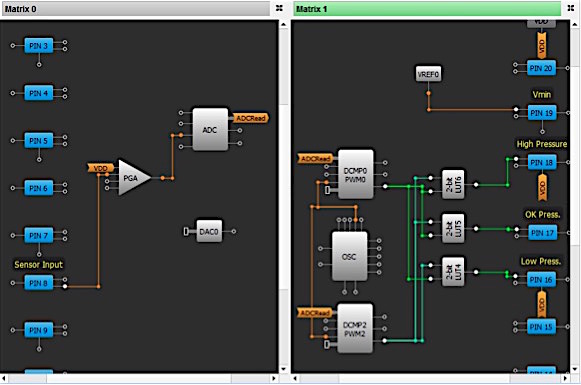
Figure 4. Pressure Measurement block diagram.
The single-ended signal from the sensor is obtained from PIN 8, which connects to the input of the PGA. The PGA configuration is shown in Figure 5. It shows the PGA configured in Single-Ended Mode with a Gain of 4 and it’s always powered on.
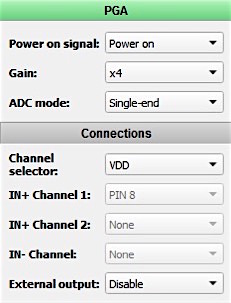
Figure 5. Programmable Gain Amplifier configuration.
The output of the PGA is connected to the Analog to Digital Converter. The configuration of the ADC is a single-ended mode, with the RC oscillator as the ADC clock as shown in Figure 6. With this clock configuration, the ADC sample rate is 1.56 ksps.
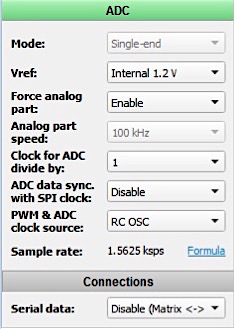
Figure 6. ADC configuration.
The ADC conversion is analyzed with the DCMP/PWM blocks. DCMP0 compares the pressure with the low limit, indicating when the pressure is lower than the configured value with a low level on its OUT+ output. The DCMP/PWM 0 block is configured as DCMP, comparing the positive input with the value stored in Register 0.
DCMP2 compares the pressure with the high limit, indicating when the pressure is higher than the configured value with a high level of its OUT+ output. The PWM/DCMP 2 block is configured as DCMP, comparing the positive input with the value stored in Register 2.
DCMP0 configuration is shown in Figure 7. The configuration of DCMP2 is the same as the configuration of DCMP0.

Figure 7. DCMP/PWM0 configuration.
To determine the outputs of the system, 2-bit LUT4, LUT5 and LUT6 are used. LUT4 output is high only when a low pressure is detected (low level at OUT+ of DCMP0 and at OUT+ of DCMP2). LUT5 output is high only when the correct pressure is detected (high level at OUT+ of DCMP0 and low level at OUT+ of DCMP2). LUT6 output is high only when a high pressure is detected (high level at OUT+ of DCMP0 and high level at OUT+ of DCMP2). Figure 8 shows the configurations of 2-bit LUT4, LUT5 and LUT6.
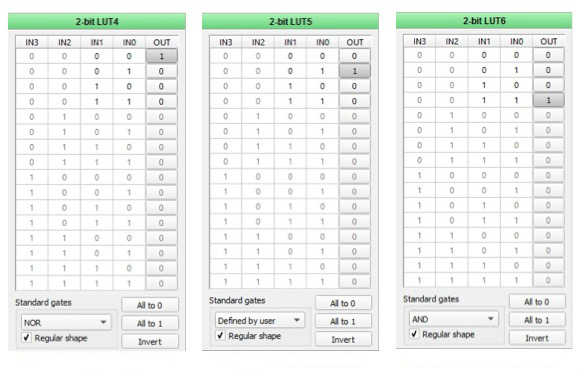
Figure 8. From left to right: LUT4 configuration, LUT5 configuration, LUT6 configuration.
The output of 2-bit LUT4 (low-pressure output) is connected to Pin 16, the output of 2-bit LUT5 (correct pressure output) is connected to Pin 17 and the output of 2-bit LUT6 (high-pressure output) is connected to Pin 18.
DAC0 is included in the design as the voltage reference Vmin. It is configured to generate 60mV and is connected to GPIO19 via the VREF0 block. Its configuration is shown in Figure 9.
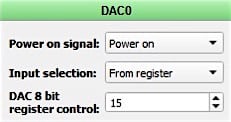
Figure 9. DAC0 configuration.
Test and Conclusions
To test the implementation, a linear ramp of pressure was applied to the sensor, from a low pressure to a high pressure along the analyzed range. To analyze the results, pins 16 to 18 (in this order) were logged with a logic analyzer. These outputs can be seen in Figure 10.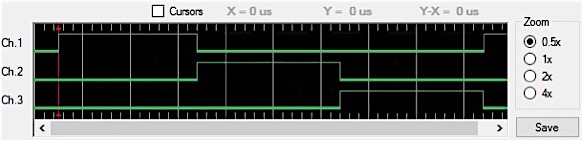
Figure 10. Pressure measurement and preprocessing outputs test.
It can be seen that the system is tested for the three possible states, obtaining a high level on the corresponding output pin of the SLG46620.
No comments:
Post a Comment