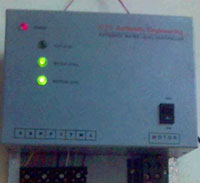
Here a simple circuit to control the Water pumps. When the water level in the over head tank exceeds the required level, the pump automatically turns off and stops the pumping process thus preventing the over flow of water. It uses a relay to cut off the power supply to the water pump.
The circuit is build using the following components:
- CMOS IC CD4001: It is a versatile 14 pin IC which contains 4 NOR gates. Each NOR gate has two inputs and one output. Thus the IC has 8 input pins and 4 output pins, one Vcc pin (connected to positive voltage supply) and one Vss (connected to negative supply). Its basic features include – Maximum supply voltage: 15V, Minimum supply voltage: 3V, Maximum speed of operation: 4MHz. It can be used in tone generators, metal detectors etc.
- Transistor BC547: It is a NPN bipolar junction transistor and it is used mainly for amplification and switching purpose. Its features include maximum current gain of 800.It is used in CE configuration when used as an amplifier.
- Battery: A DC supply of 9V is given through a battery to power up the circuit.
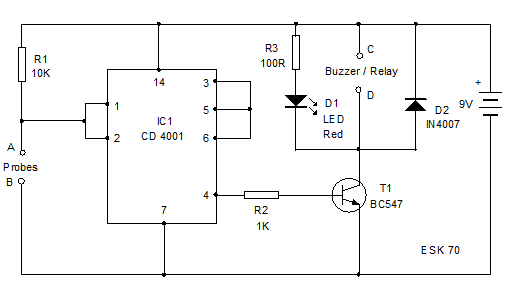
The circuit uses a CMOS IC CD 4001 /
4011 to drive the relay. Its input gate 1 is used to connect the probe
to detect the water level. One probe is connected to the gate 1 of the
IC and the other probe to the ground. When the probe A connected to the
gate 1 of IC is floating, the input of gate 1 remains high and the
output pin 4 goes high and the relay driver transistor conducts. The
relay will be activated. The power supply of the water pump is connected
through the common and the NO contacts of the relay so that when the
relay turns on, water pump works. LED indicates the working of the
relay. When the water level rises and makes contact with the probes A
and B, output of IC turns low and the relay de-energizes to stop the
pumping.
Initially when A and B are not
connected, i.e. water level is low, the input pin1 of the IC is at logic
high and according to NOR gate truth table, the output at pin3 will be
at logic low. Since pin3 is shorted to pins 5 and 6, hence the input to
other NOR gate will be logic low signals. This gives a logic high signal
to the corresponding output pin 4. As current flows through the
resistor to the base of transistor, it starts conducting and acts as a
closed switch. The relay connected to the collector of the transistor
gets energized and the NO contacts get connected to the common contact
and the water pump gets power supply from the mains and starts working.
Now when water level rises in the tank
rises such that probes A and B are connected through water, current
flows through them (As water is a conductor) and the pins 1 and 2 are
connected through A and B to the negative supply of the battery.
The output pin3 is thus, at logic high
level, causing the input pins of the other NOR gate to be at logic high
level and thus the corresponding output pin4 is at logic low level. The
transistor gets cutoff due to lack of bias current and the relay gets
correspondingly de-energized and the power supply to the water tank gets cut off.
Apart from the technique discussed
above, there can be another way to control water level in the tank by
sensing it using Ultrasonic technique. Unlike the previous method, this
does not requires any contact with the water tank.
The system consists of the following parts- A Regulated DC power supply to convert the AC supply to regulated DC voltage using bridge rectifiers and filters.
- An ultrasonic Module consisting of an ultrasonic transmitter and a receiver to sense the water level condition of the tank.
- A microcontroller which acts as a control unit.
- A transistor and a MOSFET unit which forms the switching unit
- A relay to control application of current to the pump
- A Pump which is the load
The ultrasonic sensor senses the level
of water in the tank by transmitting ultrasonic signals towards the
tank. The water in the tank reflects back the ultrasonic signals, which
are received by the receiver. The ultrasonic or the sound signal
received is converted to electric signal pulses which are applied to the
Microcontroller. These pulses denote the level of water in the tank. As
the water level decreases below certain level, the ultrasonic module
gives an indication through the electric signal and the Microcontroller
accordingly drives the transistor to off condition, which in turn causes
the MOSFET to be switched on and accordingly the relay gets energized
and the pump is switched on. In case the water level is above the
threshold level, the Microcontroller accordingly switches off the relay
through the transistor and MOSFET arrangement, so as to switch off the
pump.
This system is used only to sense the level of water in a tank and display the reading on a 7 segment display.
Here a circuit board consisting of a
parallel arrangement of conducting wires is placed in the tank. These
wires serve as input to the Priority Encoder which generates a BCD
output based on the input readings. The Priority Encoder drives a set
of transistors which in turn provide input to the BCD to 7 segments
Decoder which uses the BCD signal to drive the 7 segment LED display.
When the input unit is placed in the
water tank, current flows through the wires immersed in water and
accordingly the corresponding number of inputs is in high logic state.
The Encoder receives this input and based on the priority level of the
inputs, gives a digital output code corresponding to the input with
highest priority.
Thus if current flows through all the
wires, i.e. the tank is full; the output code will correspond to the
highest level. Here the input unit or the scale is divided into 10
levels from 0 to 9. Incase all the inputs to the Encoder are in high
state, the output is also a high logic signal which drives all the
transistors to ON condition, so that all the inputs to the BCD to 7
segment Decoder are in low logic state. The BCD to 7 segment Decoder
simply acts as an inverter and thus gives a high logic signal in all its
output and thus the highest level of 9 is displayed on the Display.
No comments:
Post a Comment